ORDER PROCESSING
The first step of the job was the development of a set of drawings that encompassed everything that had been agreed and which could be sent off to their factory for manufacture.
This included
design details, like the colour of the internal gaskets, the exact sizes of the different frames in a window and obscure glass choice. It was worth my detailed study as one of the windows had the opening frame on the wrong side because of a different view being used and some extra materials had been included that we didn’t need.
Finally, the formal contract was signed, and a target installation date was agreed.
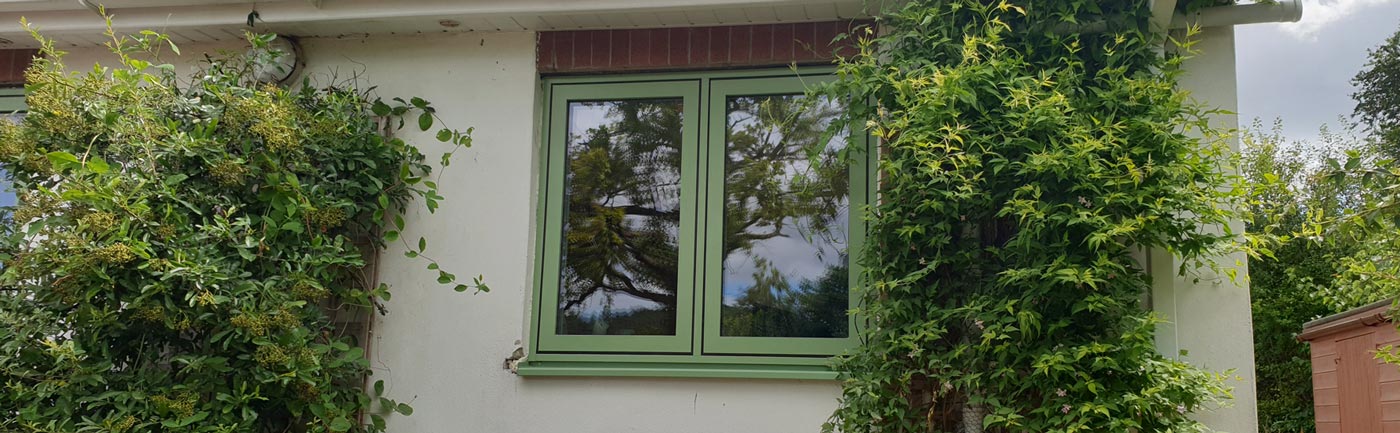
Design details: finalising the colour choice, glass type and frame size during the order processing period
INSTALLATION
On the morning of the rescheduled installation date, the team of 4 fitters arrived together with a large lorry carrying all the windows and doors. The first task was to unload, and it was immediately clear that these were substantial, heavy frames. Thankfully, the lorry had an onboard crane and was able to lift the heaviest frames over the hedge from the grounds next door. All the frames were well protected and undamaged – indeed, I saw no frame damage throughout the whole installation.
We were very happy with the quality of the installation.
The damage to the render surrounds was minimal, although we hadn’t appreciated that the new external aluminium window sills wouldn’t extend wider than the window frames, unlike the old windows. This left holes either side of the window sills that would need to be filled at a later date.
The windows fitted the holes tightly and the use of expanding foam was relatively limited compared to some installations I have seen. Great care was made to cut the tiles back in the bathrooms and kitchen (because the new frames are thicker than the old ones) and only 2 tiles were damaged.
Several subsequent observers commented that the installers had done a great job, which reinforced our supplier decision.

FENSA CERTIFICATE
Norrsken is a registered FENSA installer which provides a guarantee of compliance with Building Regulations. An inspector visited our property and a certificate of compliance has been issued.
THE RESULT
While the project took considerably longer than expected this was primarily due to the Covid-19 pandemic. From first supplier discussions to completion took almost 1 year.
The change has been transformational.
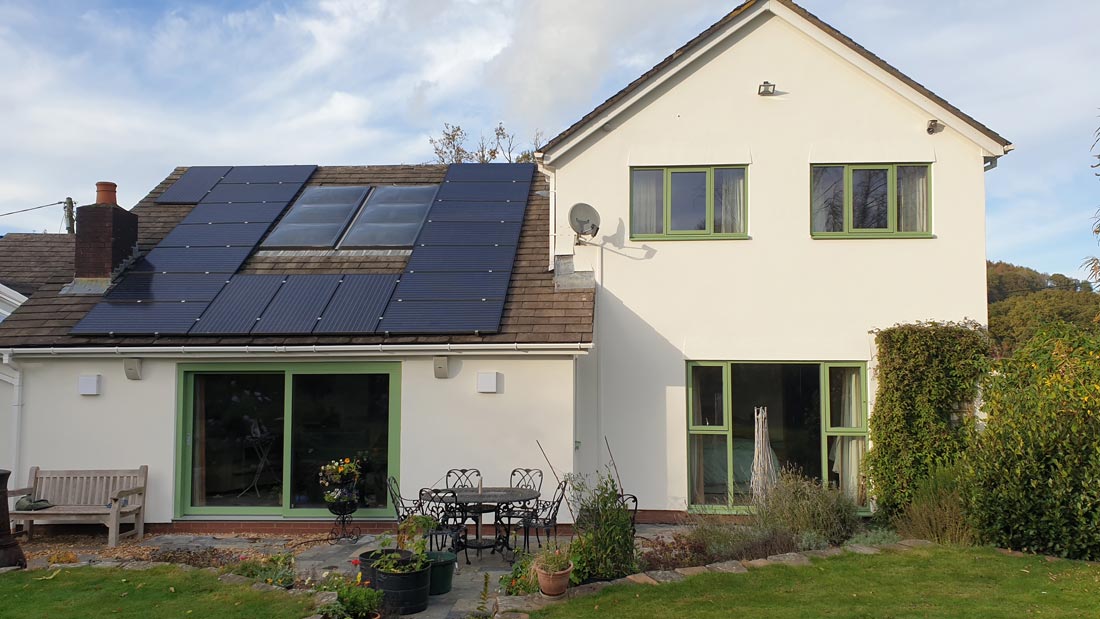
The finished project: We had the entire house repainted and re-rendered, giving it a beautiful clean look and a new lease of life.
Gone are the tired windows and green stained walls. In their place we have a fresh, clean, modern looking house that we hope will be relatively maintenance free for many years. It wasn’t cheap, but came in close to my initial uneducated back of the envelope estimates. Overall, I think we got a very good deal, and could have paid considerably more. It was definitely worth taking the time to understand the market and options, and negotiating the best deal we could.
I would have no hesitation recommending Norrsken.
INSURANCE BACKED GUARANTEE
Unfortunately, Covid-19 put the project on hold for approx. 3 months. While I understood the situation, I was uncomfortable about Norrsken holding my deposit and potentially losing it if the company experienced trading difficulties. Thankfully, Norrsken was happy to purchase an Insurance Backed Guarantee to cover the contract and allay my fears.
Before and after: tired and decaying vs. beautiful, high-performance, low maintenance windows
WINDOW BOARDS
As the old window boards didn’t match the new windows (and a large number had been cut out as part of the replacement process) we took the opportunity to fit new window boards throughout. I had expected to be able to buy off the shelf boards but after being unable to source ones to match the detail required, I turned to a friend who runs a small workshop for advice. He offered to source, cut and lacquer the boards – an offer we quickly and gratefully accepted.
We lacquered the boards after using a wood stain purchased from Norrsken, the same stain that had been used on the window frames, and the final result is excellent. It does mean, though, that each room now needs to be redecorated to hide the resulting plastering around the window board holes/gaps.
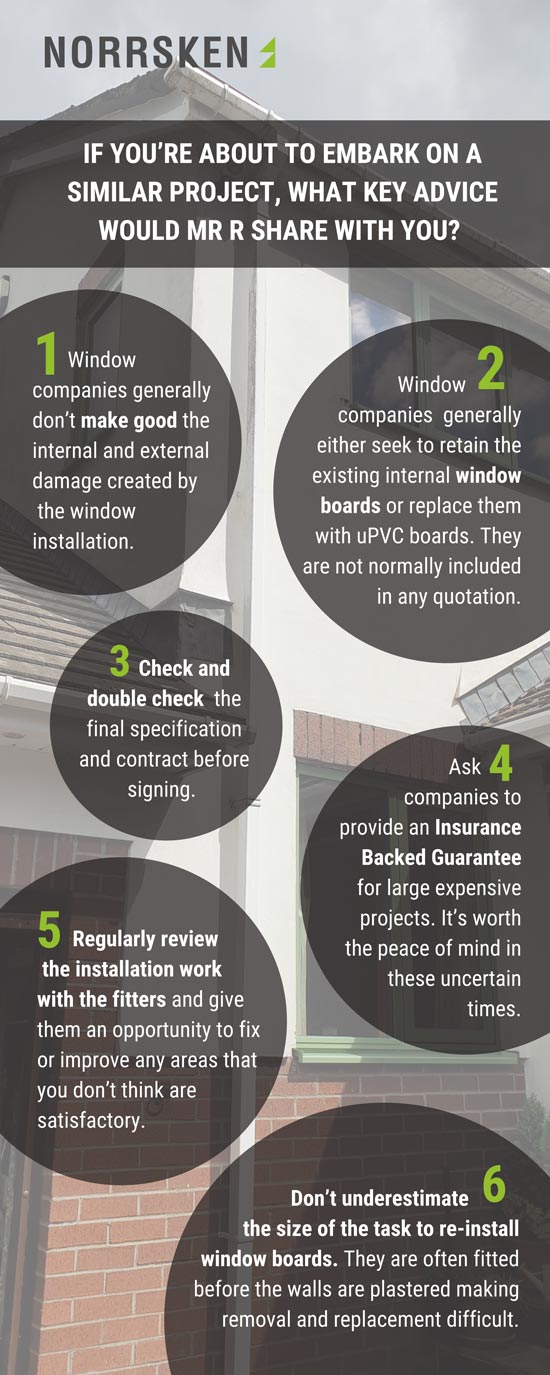