Including trickle vents in every new window is not mandatory - but you are pretty likely to need them - unless you’re installing MVHR.
Why? As mentioned earlier, replacing your windows is likely to make your home more airtight. If you’re not installing an MVHR system, then increased airtightness will reduce (beneficial) ventilation in your home. The building regulations require ventilation to be no worse than it was before the work was carried out and to meet EA requirements. This can be demonstrated in any of the following ways:
- Installing replacement windows with trickle vents that satisfy requirements in Table 2
- If the dwelling will have continuous mechanical extract ventilation, installing background ventilators according to requirements at the bottom of Table 2.
- Other ventilation provisions, if it can be demonstrated to a building control body that they comply with the Building Regulations for a whole dwelling via a combination of extract, whole dwelling and purge ventilation and do not worsen the ventilation of the building.
In practice, these EA requirements are likely to be more demanding than your existing ventilation provision, so you may end up needing to add trickle vents to openings that didn’t previously have them in order to meet minimum requirements.
HOW MANY TRICKLE VENTS DO I NEED?
The total number of ventilators installed in the dwelling’s habitable rooms and kitchens should be at least the following.
- Four ventilators if the dwelling has one bedroom.
- Five ventilators if the dwelling has more than one bedroom.
The minimum total area of background ventilators in each room should follow the guidance in the Table below.
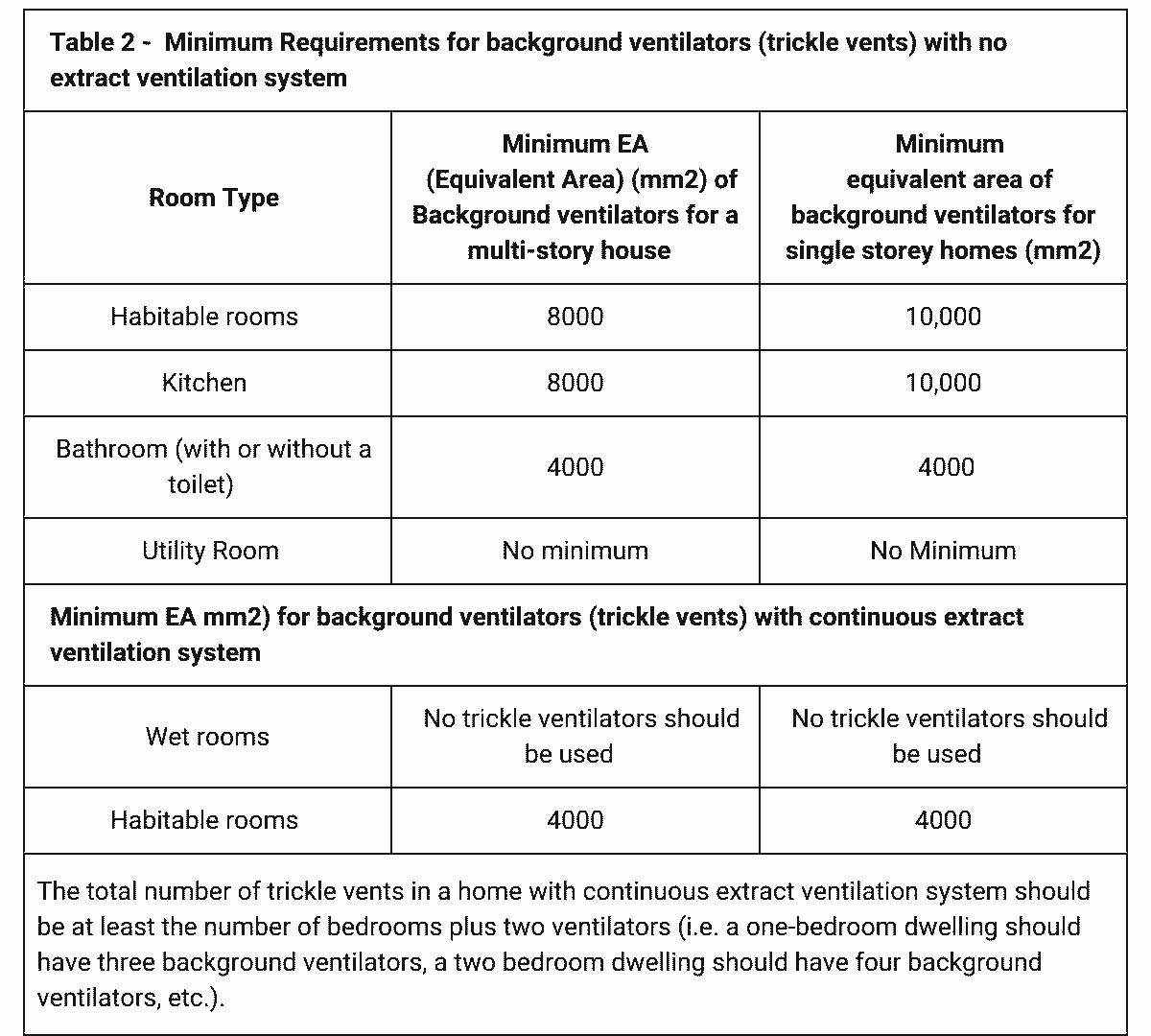
This guidance has a few exceptions:
Where a kitchen and living room are open plan, at least three ventilators of the same equivalent area as for other habitable rooms should be provided within the open-plan space.
If the dwelling has 70% or more of its openings on the same facade, or its kitchen has no windows or external facade through which a trickle vent can be installed, Table 2 doesn’t apply. You should seek expert guidance.
I’M INSTALLING A FORM OF CONTINUOUS EXTRACT VENTILATION. DO I STILL NEED TRICKLE VENTS?
Continuous extract ventilation describes several different types of ventilation system, including mechanical extract ventilation (MEV), Mechanical ventilation with Heat Recovery (MVHR) and Positive Input Ventilation (PIV).
Most continuous extract ventilation systems remove humidity and waste air, but don’t supply fresh air, so trickle vents are still needed. A notable exception to this is MVHR.